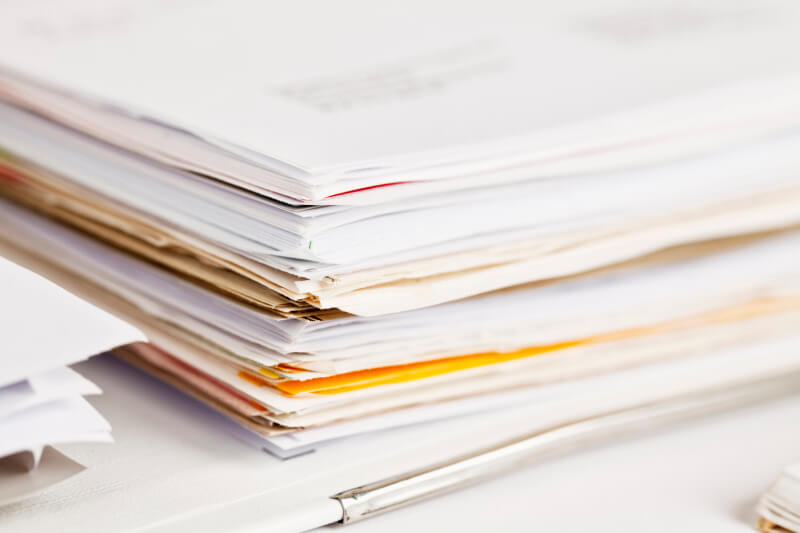
CHROME-X®
In plastic injection molding, the surface of the tool is constantly exposed to material adhesions, which influence the surface quality of the manufactured plastic components. The new coating solution from eifeler offers ideal protection for the preservation of highly polished tool surfaces to produce plastic parts with a defined and constant surface quality. Therefore, the new CHROME-X® contributes to an improved the surface quality of plastic parts.
Since many plastic components constitute a mass-product, the fundamental challenge is to ensure a consistent surface quality over numerous production cycles. Improved demolding and minimization of material adhesions represent key features for the reduction of cycle times or maintenance work and eventually for an optimized quality of the plastic part. Furthermore, with complex structured plastic mold surfaces there is a challenge in reproducing the image accuracy of the texture, especially over several injection cycles.
Compared to arc evaporated PVD coatings, the CHROME-X® by eifeler is magnetron sputtered and offers numerous technological advantages. CHROME-X® is deposited at low temperatures (< 250 °C) and requires no post-treatment due to the dense and droplet-free coating growth.
Change in gloss on a plastic molded part compared to a molded part that was manufactured with an uncoated tool. Compared to Arc-CrN, CHROME-X® leads to an increase or preservation of gloss.
Molded ABS plastic parts, manufactured with TiN-coated (left) and CHROME-X®-coated (right) tools.
Hardness HIT | 15 – 23 GPa |
Hardness HV | 1.400 – 2.200 HV |
Coating thickness | 1 – 3 µm* |
Maximum operating temperature | 400 °C / 752 °F |
Roughness** | Ra ≤0,022 Rz ≤0,180 |
Colour | Silvery, shiny metallic |
CHROME-X®
From the idea to the solution
The CHROME-X® coating was developed specifically for the preservation of highly polished surfaces in plastic injection molding. Using the sputtering technology, a near-net-shape and almost defect-free surface with a minimized roughness profile is generated, which can reproduce plastic components with a predefined gloss level and consistent quality over several manufacturing cycles. An almost invisible protective film with a decisive influence on the final molded plastic part!
Dr.-Ing. Alexander Fehr, PVD Forschung & Entwicklung bei voestalpine eifeler Vacotec GmbH
Technical application support
Düsseldorf
T: +49 211 97076-0
F: +49 211 97076-955
Technical application support
Ettlingen
T: +49 7243 5778-0
F: +49 7243 5778-20
Technical application support
Schnaittach
T: +49 9153 9227-0
F: +49 9153 9227-65
Technical application support
Salzgitter
T: +49 5341 2232-0
F: +49 5341 2232-14