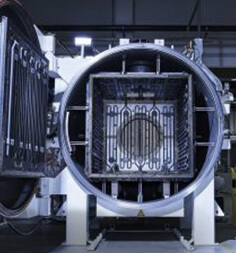
Your expert for heat treatment
Controlled heat treatment gives your tool optimum mechanical properties, reduces subsequent machining and makes it more robust in daily use.
The positive effect: The service life of tools increases, investment and maintenance costs decrease.
We offer many years of experience in the heat treatment of die cast inserts as well as special materials, cold and hot work steels, plastic mold and high-speed steels and PM steels. We offer a wide range of treatments to achieve the optimum result for our customers: from vacuum heat treatments such as vakuum hardening, tempering and deep-freezing to inert gas processes and specified annealing processes.
We are certified in accordance with DIN EN 9100, ISO 9001:2008 and meet the NADCA and Ford standards for die-cast inserts. We are also NADCAP-certified (PVD coatings).
Processes such as low-pressure carburizing, inductive hardening, flame hardening, gas nitriding processes and many more round off our range of treatments in cooperation with well-known sub-suppliers.
Vacuum hardening
In vacuum hardening, components and tools, usually made of high-alloy tool steel, are heated in a vacuum chamber in a controlled manner and quenched with nitrogen overpressure and thus hardened.
The vacuum prevents reactions on the steel surface that could lead to oxidation or edge decarburization. The precisely adjustable cooling flow also has a positive influence on distortion and the risk of cracks in the hardened material.
Using state-of-the-art control technology, complex batches and tools can also be quenched with a hot bath simulation in which quenching can be briefly interrupted along exact parameters. This leads to further optimization of the quenching characteristics.
Advantages of vacuum hardening:
(Vacuum) tempering is a low-temperature process that is carried out after hardening the steel in order to achieve the correct ratio of microstructure, hardness and toughness by gradually transforming the material structure into the hardened structure (tempered martensite).
he deep-freezing of steel is a processing step in which the hardened steel is cooled to a temperature of approx. -80 to -150 °C. This serves to convert retained austenite into the hardening structure martensite. This serves to convert retained austenite into the hardened structure martensite.
Particularly in the case of ledeburitic steels and high-speed steels, this prevents subsequent undesirable structural transformations and optimizes the mechanical-technological properties of the steels for the respective application.
In precipitation hardening, also known as ageing, precipitates are generated by diffusion at relatively low temperatures (up to approx. 500 °C). The higher the temperature, the faster the diffusion and thus the transformation from single-phase solid solutions into two-phase alloys.
Solution annealing is used for austenitic steels. The non-hardenable austenitic steels precipitate uncontrolled carbides during hot forming, which can lead to intercrystalline corrosion or even cracks during further processing or later use. The abrupt quenching from the annealing temperature causes these carbides to dissolve and prevents them from precipitating again. In addition, solution annealing has a recrystallizing effect on a cold-formed matrix and thus serves to reduce stresses, such as those that can arise during cold forming of these steels.
As a result of plastic deformation or plastic or machining processes, stresses arise in the material that can subsequently lead to undesirable and uncontrolled dimensional changes. In order to reduce these stresses in the structure of the steel and the undesirable changes to the workpiece, stress relief annealing can be carried out after (e.g. rough machining). Here, the workpiece is slowly heated at temperatures between 480 °C and 650 °C, held for approx. 2-3 hours and then slowly cooled in the furnace or in still air.
The aim of soft annealing is to make the material as soft as possible in order to ensure the best possible processing.
For the hardening process, the soft-annealed structure of a steel also forms the optimum starting point for achieving a homogeneous hardening structure while simultaneously reducing the risk of cracking during the hardening process.
A protective gas or vacuum furnace is generally used for soft annealing. Higher alloyed steels with a carbon content >0.30 – 0.35 % are normally soft annealed, as hypoeutectoid steels with a very low carbon content are considered to be very soft anyway and additional soft annealing can make machining more difficult.
Copper and brass alloys can also be soft annealed, e.g. after cold forming.
Depending on the steel grade, the annealing temperatures are between 700 °C and 900 °C, and between 300 °C and 650 °C for copper and brass alloys.
The respective annealing temperature here is just above the A1 transformation line (PSK). The aim is to enable diffusion processes to transform the cementite lamellae into spherical and therefore homogeneous and easy-to-process cementite.
Typical materials:
Plasma nitriding is one of the thermo-chemical heat treatment processes. Here, a wear and corrosion-resistant protective layer is created near the surface by adding nitrogen.
With this low-distortion heat treatment at relatively low temperatures, up to a maximum of 600 °C, high-alloy materials in particular are given an abrasion-resistant protective coating that improves wear protection while also improving corrosion protection. Partial treatment is also possible by covering defined areas.
In order to be able to finally subject the tools to a PVD or CVD coating, it is possible to set a diffusion zone without a compound layer during plasma nitriding.
During plasma nitrocarburizing, carbon also diffuses into the surface of the material. The advantage is that materials that have not been pre-tempered can also be surface hardened using this process.
Plasma treatment
At voestalpine, experts in steel and heat treatment work together to create the best solutions for our customers. For me, it is always the greatest reward when the service life increases after professional hardening and our customers save time and money.
Andreas Schuppart, Manager Heat treatment Region Germany